In the different applications of Oilfield Polyacrylamide, what differences exist in the selection of emulsifiers?
In various applications of Oilfield Polyacrylamide, the choice of emulsifiers does indeed differ. This is primarily because different applications have varying requirements for the stability and performance of emulsifiers.
In the application of drilling mud additives, emulsifiers need to possess excellent stability to ensure the stable suspension and dispersion of drilling mud. Emulsifiers with strong interfacial activity and good wetting properties are typically chosen to disperse and control solid particles in the mud more effectively.
In hydraulic fracturing fluids used in oilfield development, Oilfield Polyacrylamide is primarily used to enhance the permeability of oil reservoirs. Emulsifiers for this purpose need to have low interfacial tension to facilitate the uniform dispersion of components in the fracturing fluid. When selecting emulsifiers, considerations also include their shear resistance and thermal stability to ensure good stability even under high temperatures and shear forces.
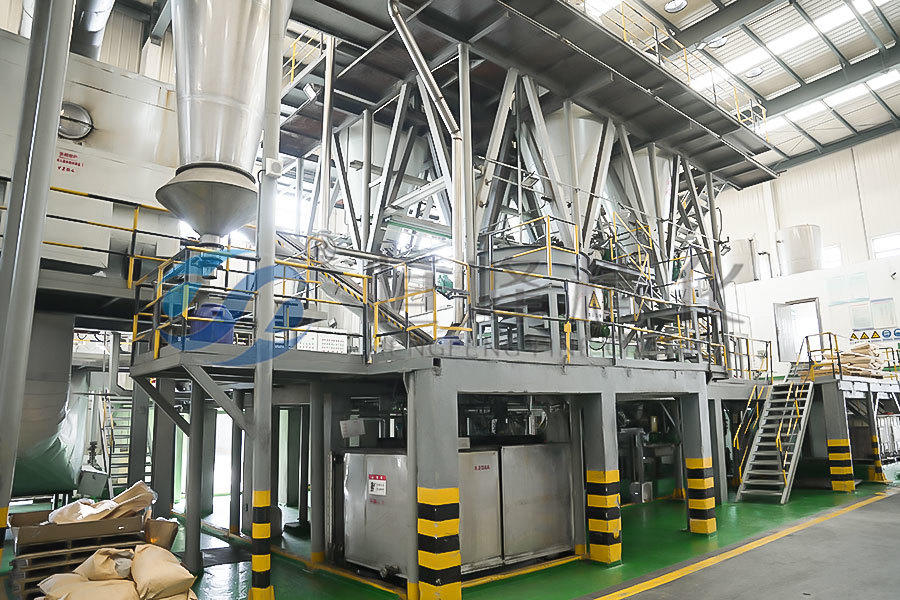
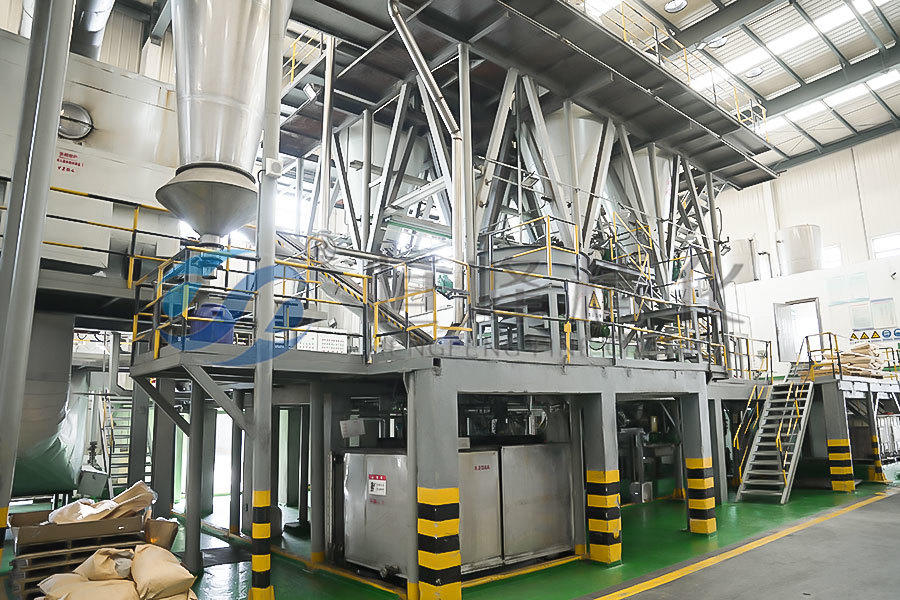
In tertiary oil recovery methods, the choice of emulsifiers is crucial for increasing the recovery rate. Emulsifiers need to be able to form stable emulsions with crude oil to effectively extract crude oil from rock surfaces. When selecting emulsifiers, factors such as their compatibility with crude oil, ability to reduce interfacial tension, and effectiveness in increasing the recovery rate need to be considered.
For the use of Oilfield Polyacrylamide in waterflooding or polymer flooding processes, the selection of emulsifiers needs to consider their impact on the water/oil interface and their ability to enhance oil recovery efficiency. Emulsifiers should have the ability to reduce water phase permeability and increase the viscosity of displacement agents to improve the recovery rate of crude oil.