How do different types of fracturing fluid chemicals impact the efficiency and effectiveness of fracking operations?
Hydraulic fracturing, commonly known as fracking, has revolutionized the energy industry by unlocking vast reserves of oil and natural gas from deep underground formations. Central to the success of fracking operations is the use of fracturing fluid chemicals, a complex mixture designed to create and maintain fractures in the rock formation, allowing for the extraction of hydrocarbons. However, the choice of fracturing fluid chemicals plays a pivotal role in determining the efficiency and effectiveness of these operations.
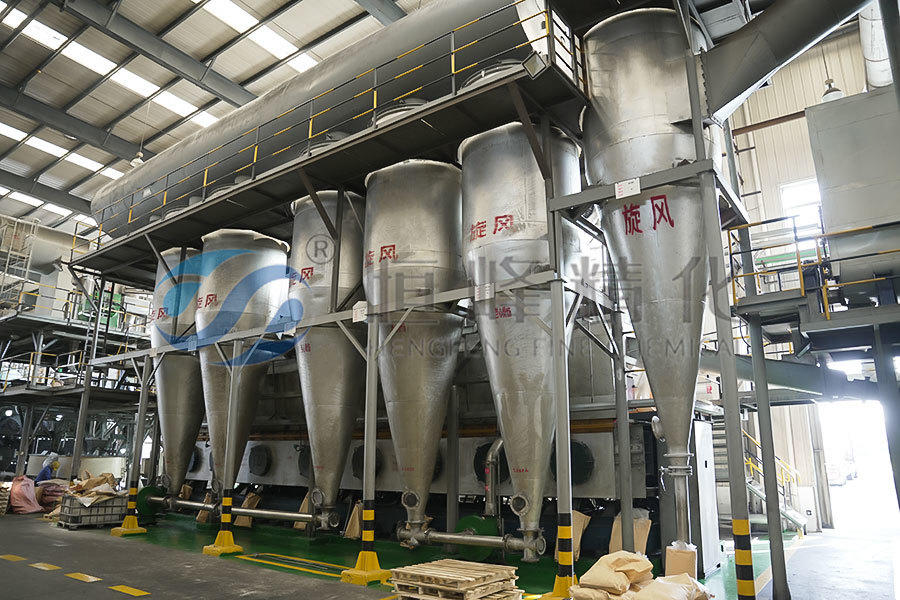
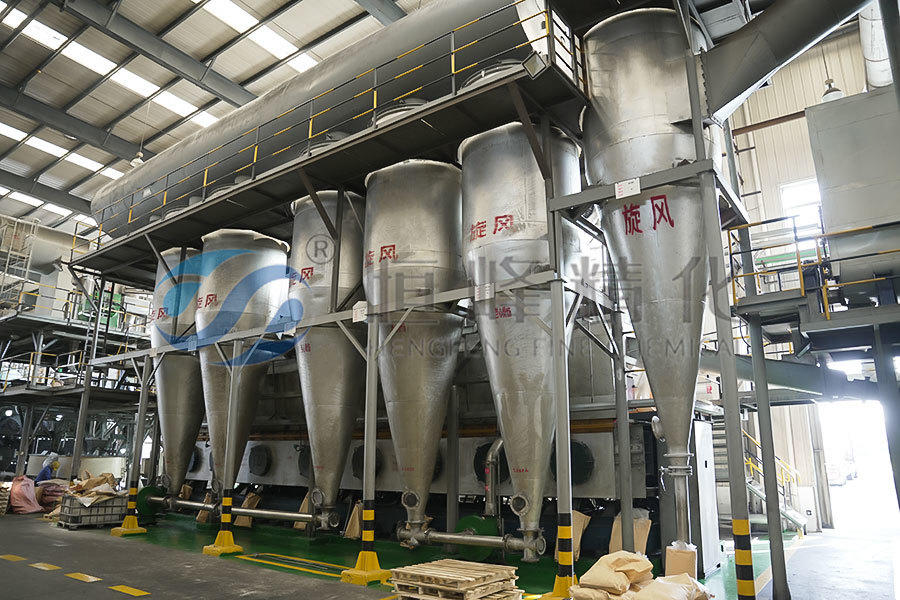
1. Viscosity and Fluid Mobility
Fracturing fluids are tasked with carrying proppants deep into the fractures to hold them open and allow for the flow of hydrocarbons. The viscosity of the fluid directly impacts its ability to suspend and transport proppants effectively. Chemical additives are employed to control viscosity, ensuring optimal proppant placement. Too high viscosity can lead to proppant settling, while too low viscosity can result in inadequate proppant transport, both of which can diminish fracking efficiency.
2. Fracture Propagation Enhancement
Certain fracturing fluid chemicals are formulated to enhance fracture propagation within the rock formation. By creating longer and wider fractures, these chemicals contribute to increased production rates from the well. Effective fracture propagation is crucial for maximizing the recovery of oil and gas resources, making these chemicals vital for operational success.
3. Clay Stabilization and Formation Damage Prevention
Many rock formations contain clays that can swell and cause blockages in fractures, reducing productivity. Fracturing fluid chemicals may include additives that stabilize clays or prevent formation damage, ensuring that fractures remain open and productive over the long term. This aspect is critical for maintaining the efficiency and effectiveness of fracking operations throughout the well's lifespan.
4. Friction Reduction
Friction between the fracturing fluid and the wellbore or formation can impede fluid movement and reduce the extent of fracture propagation. Chemical additives such as friction reducers are utilized to minimize this friction, allowing the fluid to travel more efficiently and create larger fractures. Effective friction reduction enhances the overall performance and productivity of fracking operations.
5. Water Compatibility
Fracturing fluid chemicals must be compatible with the water source used in fracking operations. Incompatible chemicals can lead to issues such as scaling, reduced effectiveness of additives, or even equipment damage. Ensuring water compatibility is essential for maintaining operational efficiency and avoiding costly setbacks during fracking activities.
In conclusion, the impact of fracturing fluid chemicals on the efficiency and effectiveness of fracking operations cannot be overstated. These chemicals play a multifaceted role in enhancing proppant transport, promoting fracture propagation, preventing formation damage, reducing friction, ensuring water compatibility, addressing environmental concerns, and optimizing cost-effectiveness. By carefully selecting and deploying the right mix of chemicals, operators can maximize production yields, extend well longevity, and navigate the complex landscape of modern energy extraction responsibly.